Ford and Hyundai to adopt aluminum casting process used by Tesla
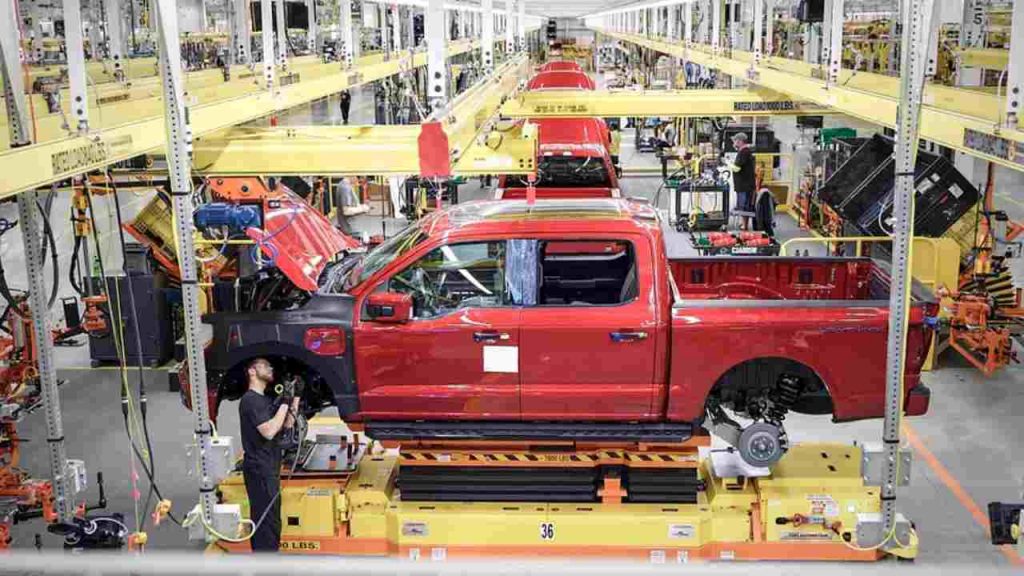
Ford Production Techniques (carbuzz.com)
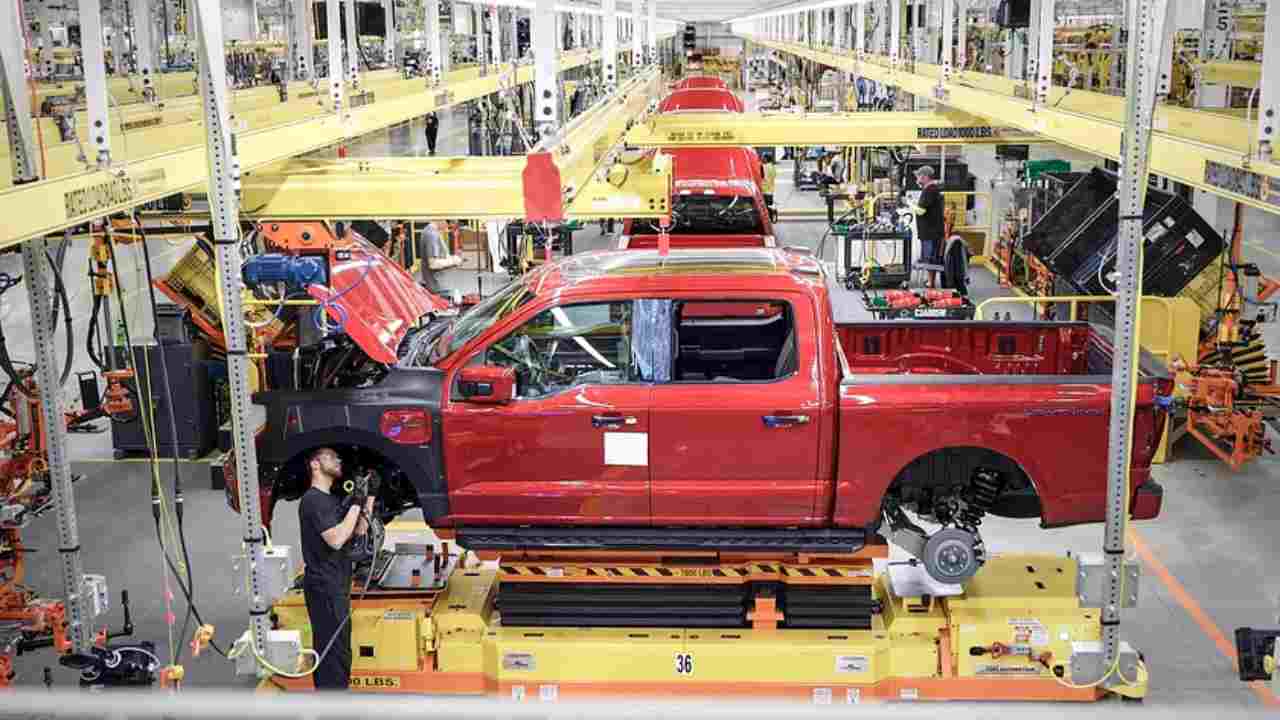
Both automakers have signed a deal with Idra, an Italian casting machine maker supplying Tesla with advanced machineries.
Ford and Hyundai have decided to implement an innovative aluminum casting process, similar to the one used by Tesla, into their production lines. Idra, an Italian casting machine manufacturer that supplies Tesla with gigacasting machinery, will also be providing the technology to Ford and Hyundai.
During a recent event held by Idra, a Ford-branded ‘gigapress 6,100’ was showcased with a clamping force exceeding 6,000 tons. Additionally, another press, known as the 9,000, was on display, representing Idra’s latest and largest model, equivalent in size to a small house. An unnamed source close to the matter indicated that the 9,000 press was intended for Hyundai. The Korean automaker plans to incorporate the hypercasting process into its operations by 2026 and aims to establish a dedicated plant for efficient electric vehicle production.
At this stage, both Ford and Hyundai will employ these casting machines primarily for research and development purposes. However, other automakers are also interested in this unique manufacturing process. An undisclosed European premium car manufacturer is preparing to sign a contract with Idra for two 9,000 presses, becoming the first Europe-based car company to do so, according to the source.
Idra is experiencing high demand for its specialized equipment. The company has already delivered 14 presses to Tesla, including two 9,000 presses that will be used in the production of the new Cybertruck. Mass production of the highly anticipated electric truck is expected to commence in early 2024. To achieve annual production figures of half a million vehicles, a manufacturer will require six gigapresses, the source added.
Tesla was the pioneer in using casting machines for vehicle production. This approach not only reduces costs but also enhances overall efficiency. Gigacasting eliminates the need for spot welding, as the chassis is now formed from just two or three larger components instead of more than 60 smaller ones, reducing costs by approximately 40%, as reported by Tesla.
The adoption of this process by Hyundai and Ford may lead to more affordable electric vehicles in the future. However, it’s unlikely to be implemented in the near term. These automakers might consider using the gigacasting process for successors to models such as the F-150 Lightning, Mustang Mach-E, and Ioniq 5.
Toyota has also embraced this method, dramatically reducing production times. The entire rear part of the chassis can now be formed in just three hours, compared to the many hours it would take to craft the same rear chassis from 86 individual parts using traditional methods.